Bolt tightening procedure for industrial steel structures
Jan 14, 2025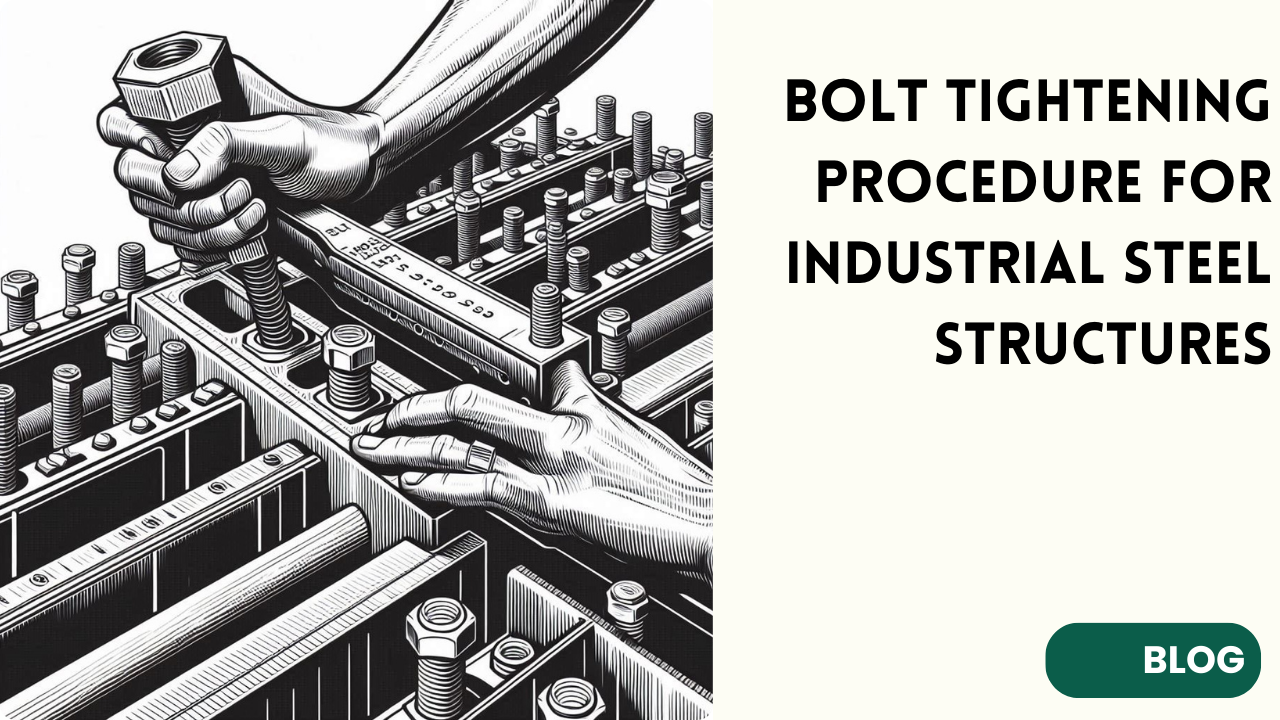
summary
The procedure for bolt tightening in industrial steel structures is a critical process that ensures the integrity and safety of bolted connections, which are foundational to the durability and functionality of various engineering applications. Bolt tightening methods include techniques such as torque tightening, turn-of-the-nut, hydraulic tensioning, and direct-tension-indicator tightening, each with its advantages and challenges. These methods aim to achieve the desired preload in bolts, which is vital for maintaining structural stability and preventing failures that can arise from improper tightening practices.
The significance of effective bolt-tightening procedures is underscored by the potential consequences of over-tightening and under-tightening, which can lead to catastrophic joint failures, particularly in high-stress environments like bridges and industrial frameworks. For instance, over-tightening can induce excessive strain on bolts, while under-tightening may result in joint loosening under operational loads.
As such, adherence to manufacturer specifications, industry standards, and quality control measures is essential to ensure the reliability of bolted joints.
Controversies surrounding bolt tightening often relate to the variability in tension achieved across multiple bolts when using different methods, which can result in inconsistencies and compromise structural integrity. Research indicates that variations can be as significant as ±30% among bolts tightened under the same conditions, raising concerns about the adequacy of conventional methods in critical applications.
Consequently, alternative techniques and tools, such as hydraulic tensioners and direct-tension indicators, are increasingly utilized to enhance precision and reliability in bolt-tightening practices. In summary, the procedure for bolt tightening is a vital aspect of industrial steel structure assembly, encompassing a range of methods and considerations that influence the effectiveness of bolted connections. Ongoing advancements in technology and a focus on best practices are essential to mitigate risks associated with improper tightening, ensuring both safety and structural performance in engineering projects.
Types of Bolt Tightening Procedures
Bolt tightening is an essential aspect of assembling industrial steel structures, ensuring the integrity and safety of the joints. Various methods and techniques have been developed to achieve proper bolt tightening, each with its advantages and limitations.
Common Bolt Tightening Methods
Torque Tightening
The torque tightening method involves applying torque to the bolt through a calibrated wrench. This technique relies on creating opposing forces to generate a torque force, which is critical for achieving the desired preload in the joint. However, this method can lead to variations in bolt tension, often ranging ±30% among bolts that are meant to be tightened equally, highlighting the challenges of achieving uniform tightening using this approach.
Turn-of-the-Nut Method
This widely used technique involves rotating the nut a specified number of turns beyond the snug-tight condition, which is the point of initial contact between the connected members. The amount of rotation required is dependent on the bolt's diameter, length, and the necessary tension.
Hydraulic Tensioning
Particularly useful for large-scale installations, hydraulic tensioning employs a hydraulic cylinder to elongate the bolt, followed by nut tightening. This technique allows for precise control over the force applied to the assembly, minimizing the variability associated with other methods.
Direct-Tension-Indicator Tightening
The direct-tension-indicator (DTI) method uses specialized washers or indicators to provide visual feedback on the tension in the bolt. This approach ensures accurate control of bolt tension and is commonly utilized in critical applications where safety is paramount.
Alternative Techniques
Heat Tightening
This less common method involves heating the bolt to induce thermal expansion, which then creates a preload as it cools and contracts. While effective for extremely large bolts, it can be challenging to measure the elongation during the cooling process, as it requires returning to ambient temperature for accurate assessment.
Strain Gauges
In this method, a small sensor is attached to the bolt to measure the deformation that occurs during tightening. By correlating the changes in the sensor's resistance to the elongation of the bolt, this technique can provide insights into the tightening tension, though it relies on established correlation tables that may not account for all variables.
Calibrated Wrench Tightening
Using a torque-controlled wrench that shuts off upon reaching a pre-set torque value, this method aims to provide a consistent tightening force. Proper calibration is essential to ensure accurate and repeatable results.
Best Practices in Bolt Tightening
Regardless of the method employed, it is crucial to ensure that the initial tightening of bolts is done to a snug-tight condition before employing any further tightening techniques. Adhering to manufacturer specifications, industry standards, and safety protocols is essential in achieving optimal results and ensuring the integrity of bolted joints. Quality control measures, including regular calibration of tools and inspection of materials, play a vital role in maintaining the effectiveness of bolt-tightening procedures.
Tools and Equipment
In the procedure for bolt tightening in industrial steel structures, various tools and equipment are utilized to ensure the accurate application of torque and tension to fasteners.
Manual and Powered Tools
Manual Wrenches
Manual wrenches are commonly used for various applications, offering a simple method of tightening bolts. These tools can provide effective and repeatable clamp loads, which is crucial for securing connections in steel structures.
Electric and Pneumatic Tools
Electric and pneumatic impact wrenches are also employed, particularly for high-volume tasks. However, while they are effective for loosening bolts, they do not provide precise control over the preload in a joint, making them unsuitable as the primary method for achieving accurate tensioning. Hydraulic torque wrenches are preferred in heavy-duty applications, providing significant torque with consistent precision.
Torque Wrenches
Torque wrenches are essential for measuring and applying specific torque values to bolts.
- Click-type torque wrenches: These wrenches emit a click sound when the desired torque is reached, indicating proper tension.
- Beam-style torque wrenches: These require the user to read a scale to determine the applied torque, often providing higher accuracy but requiring practice.
- Dial-indicating and digital torque wrenches: These offer real-time torque readings and are calibrated for high accuracy, though they can be more expensive.
Tensioning Equipment
Hydraulic Tensioners
Hydraulic tensioning methods utilize hydraulic force to apply precise tension to bolts, making them ideal for critical applications where exact clamping forces are essential. The procedure involves using a hydraulic tensioner or nut to stretch the bolt axially, allowing for uniform clamping force across multiple joints if necessary. This method ensures that each fastener experiences the same load, which is vital for structural integrity.
Shear Wrenches
For tension control bolts, a specialized electric shear wrench is used. This tool holds the nut while rotating the bolt tip, fracturing the tip upon achieving the correct preload. This method allows for effective and repeatable clamp loads, similar to traditional tightening methods.
Automation in Bolt Tightening
Loading and Positioning
Automated systems can enhance efficiency by loading nuts and bolts into machines using methods like vacuum suction or robotic arms. Positioning is achieved using pneumatic actuators or servo motors, ensuring accurate placement.
Inspection Tools
Visual inspections and specialized tools, such as torque clicker wrenches, are employed to verify the integrity of the bolt connections. Regular calibration of tools is crucial to maintain accuracy and reliability.
Steps in Bolt Tightening Procedure
Initial Tightening
The bolt-tightening process begins with an initial phase known as "snug-tight" tightening. During this stage, bolts are tightened using manual or impact wrenches until they are snug but not fully torqued. This initial step is crucial as it prepares the bolts for the subsequent tightening stages and ensures that the assembly components are properly aligned.
Final Tightening Methods
After the initial snug-tight stage, bolts require further tightening to meet specified torque levels.
Turn-of-Nut Method
One common approach is the turn-of-nut method, which involves turning the nut into a specified angular rotation after achieving snug tightness. This method enhances the accuracy of bolt elongation and preload, contributing to a more secure fastening.
Calibrated Wrench Method
Another widely used technique is the calibrated wrench method. This involves using calibrated torque wrenches to apply a specified torque value, ensuring that each bolt achieves the desired tension. This method is particularly important as it helps to avoid over-torquing or under-torquing, both of which can lead to structural failures.
Quality Control and Safety Measures
Throughout the tightening process, quality control and safety measures are essential. It is recommended to regularly inspect tightening procedures to ensure compliance with industry standards. Additionally, technicians should be trained on proper torque techniques and the importance of following manufacturer specifications for optimal performance.
Additional Considerations
It is important to consider various factors that can influence torque application, including friction coefficients, lubrication effects, and the specific geometry of the assembly. Proper understanding of torque principles is vital to maintaining the integrity of bolted joints and ensuring operational safety.
By adhering to these outlined steps and methods, the bolt-tightening procedure for industrial steel structures can be effectively executed, minimizing the risk of equipment failure and ensuring the reliability of structural assemblies.
Factors Affecting Bolt Tightening
Bolt tightening is a critical process in ensuring the integrity and performance of industrial steel structures. Several factors influence the effectiveness and reliability of the tightening process, including the choice of the tightening method, the conditions of the materials involved, and the specific practices employed during installation.
Bolt Tightening Methods
The selection of the appropriate bolt-tightening method plays a significant role in achieving optimal preload and minimizing variability. Methods such as heat tightening, hydraulic tensioning, and tension indicating techniques each have their advantages and limitations. For instance, heat tightening relies on the thermal expansion of the bolt, which can be effective but also presents challenges in measuring the bolt's length accurately during the cooling phase. Hydraulic tensioning, while useful for large-scale installations, can lead to variations in tension of up to ±30% between bolts, even when tightened using the same method.
Material Considerations
The characteristics of the bolts and the materials they are fastening also affect the tightening process. For example, corrosion can weaken steel structures, leading to loss of material and compromised load-bearing capacity. The yield strength of steel is influenced by its chemical composition and the heat treatment it undergoes, which must be considered when selecting bolts for specific applications. Ensuring that the materials used are suitable and meet the required specifications is essential for maintaining structural integrity.
Environmental Factors
Environmental conditions such as moisture and temperature can also impact the effectiveness of bolt tightening. For example, structures exposed to repeated wet-dry cycles are more susceptible to corrosion, which can lead to increased friction and decreased preload efficiency. Additionally, temperature fluctuations can affect the material properties of the bolts and the structural components they connect, necessitating adjustments in the tightening procedure.
Installation Practices
Best practices in bolt installation, including the sequence and technique of tightening, significantly influence the performance of bolted joints. Following an organized tightening sequence helps prevent localized stress concentrations and ensures an even distribution of forces across all bolts. It is recommended to consult OEM specifications for the appropriate sequence and torque values and to use calibrated tools for precise torque control. Techniques such as alternate direction tightening and final torque checks can further enhance the effectiveness of the tightening process. By understanding and addressing these factors, engineers can optimize the bolt-tightening process, thereby enhancing the reliability and longevity of industrial steel structures.
Quality Control Measures
Quality control is a critical aspect of bolt tightening procedures in industrial steel structures, ensuring that all connections meet safety and performance standards. Effective quality management involves several key practices to prevent failures and ensure the integrity of bolted connections.
Pre-Installation Inspection
Before installation, a thorough inspection of bolts and associated components is essential. This includes verifying the mechanical properties of the fasteners, ensuring they comply with relevant standards such as ISO 898-1 and ASTM F606. Proper surface preparation of both the bolt and the mating surfaces is also crucial, as contaminants can adversely affect the connection's strength.
Installation Procedures
During the installation phase, quality control measures must be enforced to ensure that the correct tightening techniques are applied. This includes using calibrated tools and equipment designed for bolt tightening, such as torque wrenches and electric turn-of-nut tools, which provide precise control over the tightening process. Inspections should be conducted to confirm that bolts are installed as per the manufacturer’s requirements, and critical connections must be checked according to an established inspection and test plan.
Verification and Testing
After installation, bolts should undergo verification testing to confirm that they have been tightened to the specified preload levels. Techniques such as bolt tension calibration and non-destructive evaluation (NDE) methods—including ultrasonic, magnetic particle, and dye penetrant inspections—are employed to assess the integrity of the bolts without damaging them. Load testing may also be conducted to confirm that bolts can withstand the operational stresses expected in service.
Continuous Monitoring
Ongoing monitoring of bolting activities is essential for maintaining safety and performance standards. This includes checking that all personnel are wearing appropriate personal protective equipment (PPE) and that safety devices, such as warning signs and barriers, are in place to protect workers on site. Regular audits of bolting practices and equipment will help identify any deviations from the quality control protocols, enabling timely corrective actions to be taken.
Training and Competence
Finally, the competence of personnel involved in bolt tightening is paramount. Comprehensive training programs should be implemented to educate workers on the properties of different fasteners, the use of bolting tools, and the application of correct tightening techniques. This investment in training ensures that personnel are equipped to perform their tasks safely and effectively, thereby minimizing the risk of installation errors that could compromise structural integrity. By adhering to these quality control measures, industrial projects can significantly reduce the likelihood of bolt failures, thereby enhancing the overall safety and durability of steel structures.
Common Issues and Solutions
Over-Tightening and Under-Tightening
Both over-tightening and under-tightening of fasteners can lead to significant joint failures in industrial steel structures. Over-tightening often occurs when installation procedures are unclear, leading to excessive strain on bolts and potential structural failures. It is essential to specify tightening criteria in plans and ensure proper lubrication to reduce friction and prevent misapplication of force. On the other hand, under-tightening typically results from inadequate specifications and insufficient lubrication, leading to the risk of joint loosening under operational loads. To mitigate these issues, adhering to specified torque values is crucial for achieving the correct preload, which is fundamental to joint integrity.
Inspection and Test Plans
The implementation of robust Inspection and Test Plans (ITPs) is vital in ensuring the correct installation of critical fixings such as tension control bolts. These plans should detail procedures for the inspection of bolted connections, particularly in high-stress applications like bridges, where failures can have catastrophic consequences. For instance, the CROSS-UK report 1185 highlighted issues with blind bolts of incorrect lengths leading to unsafe bridge structures, emphasizing the need for thorough inspections during the installation and maintenance phases.
Best Practices for Bolt Tightening
To prevent issues related to both over-tightening and under-tightening, several best practices should be followed:
- Consult Specifications: Always check the Original Equipment Manufacturer (OEM) specifications for the recommended tightening sequence and torque values.
- Controlled Torque Application: Utilize calibrated torque wrenches to ensure that preload is applied precisely, avoiding sudden spikes that could lead to joint failure.
- Tightening Sequence: Implement a systematic tightening sequence, such as a star pattern, to promote even clamping and reduce stress concentrations in the joint.
- Recheck Torque: Perform a final pass to confirm all bolts are properly tightened, ensuring that no torque loss has occurred due to material settling or deformation.
Environmental and Economic Implications
Improper tightening practices not only pose safety risks but can also have detrimental environmental consequences. Failed fasteners in structures can lead to leaks and spills, impacting surrounding ecosystems.
Additionally, the financial ramifications of over-tightening include increased long-term maintenance costs due to frequent repairs and operational downtime.
Therefore, prioritizing effective tightening procedures is not only a matter of structural integrity but also an important consideration for environmental and economic sustainability. By incorporating training programs that emphasize proper fastening techniques and ongoing education on the latest advancements, organizations can foster a culture of safety and precision in industrial operations.
Case Studies
Analysis of Bolted Joint Failures
The investigation of bolted joint failures often involves a systematic approach to understand the root cause and prevent future occurrences. For instance, a customer experienced repeated failures in a bolted assembly despite replacing the original components with new bolts, nuts, washers, and spacers. The use of spacers was intended to enhance clamp length, but the same failure recurred after the machine operation resumed. In this case, a thorough analysis was conducted, which included the collection of photographs of the damaged components and securing the environment around the failure site to prevent contamination.
Utilizing methods like the Ishikawa (fishbone) diagram, engineers can categorize potential causes of failure, ranging from design flaws to material inadequacies. This structured approach helps in identifying specific areas for improvement and contributes to a more robust understanding of the assembly's performance under load.
Technological Innovations in Bolting
The evolution of bolting technology has played a significant role in addressing the challenges associated with bolted joints. Recent advancements, including intelligent bolting systems and automated tightening processes, have improved accuracy and safety in various applications. For example, employing ultrasonic technology can enhance the reliability of bolt tightness, ensuring that assemblies maintain their integrity under operational stresses.
Furthermore, a case study highlighted the benefits of increasing the outside diameter of threaded parts, utilizing coarse pitch designs, and selecting materials with high Young's modulus to mitigate failure risks in high-stress applications. These changes not only optimize performance but also reduce the likelihood of future failures, emphasizing the importance of innovative solutions in bolting technology.
Training and Best Practices
Continuous education and training of personnel on proper fastening techniques are critical for ensuring the safety and reliability of bolted connections. For instance, comprehensive training programs should cover the significance of adhering to torque specifications and the proper use of torque wrenches. By empowering technicians with knowledge about the risks of over- and under-tightening, organizations can significantly enhance operational safety and component longevity.